Contents
塑料注塑成型是一种通过将熔融材料注入模具来生产零部件的制造工艺。其基本原理是将塑料原料加热至熔融状态后,在高压作用下将其注入模具型腔,经过冷却固化后形成预定形状的制品。
该工艺具有显著的技术优势:首先,其高效性可实现大规模连续性生产,单位成本随产量提升显著降低;其次,在复杂结构成型能力方面,能够精准复现微细特征、薄壁结构以及精密配合面等传统加工工艺难以实现的三维造型。这种特性使其成为精密工程塑料件制造的首选方案,广泛应用于汽车、电子、医疗器械等多个工业领域。
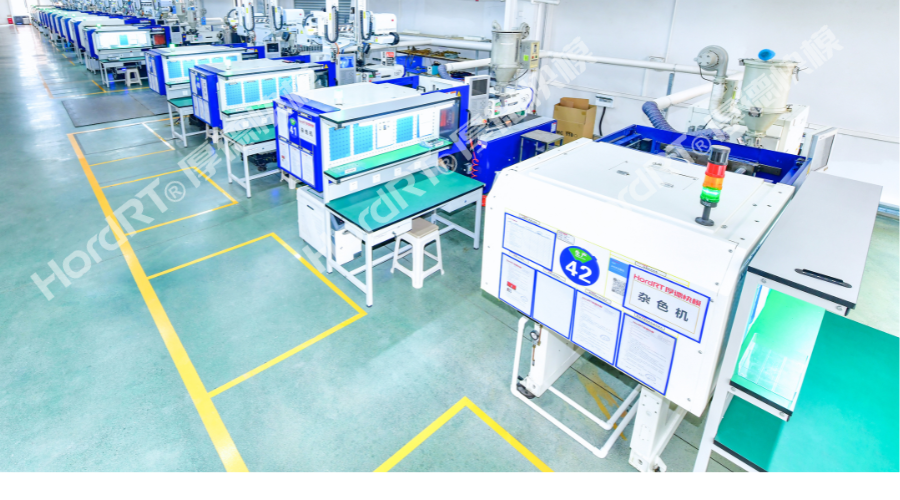
塑料注塑成型工艺流程
塑料注射成型工艺包括多个关键步骤,每一步都必须精细管控,以确保产品质量和生产效率的最优化。
第一环节:材料选型
作为工艺基础,材料选择需遵循"性能适配"原则。工程塑料的机械强度、耐热指数、流动特性等参数须与产品工况精准匹配。以丙烯腈-丁二烯-苯乙烯共聚物(ABS)为例,其兼具高强度(拉伸强度≥40MPa)、优异抗冲击性(缺口冲击强度≥20kJ/m²)及良好加工流动性,因而在汽车仪表板(公差要求±0.15mm)、电子设备外壳(壁厚1.2-2.5mm)等领域占据主导地位。美国化学理事会研究数据显示,ABS在汽车零部件市场的应用占比达32%,充分验证其工程适用性。
第二环节:模具设计
模具作为成型系统的"精密母体",其设计需实现四大技术平衡:
热力学平衡:冷却流道采用随形设计,确保模温梯度≤3℃/cm
流体力学平衡:多腔模具采用H型流道布局,熔体充填时间差<0.05s
结构力学平衡:模芯采用P20模具钢(硬度HRC 30-34),模架配置四导柱支撑
工艺平衡:浇口位置遵循"最短流动路径"原则,通常采用扇形浇口设计
通过先进的CAD/CAE系统,可实现模流分析精度达±0.8%,显著降低试模次数。
第三环节:注塑成型过程
精密注塑遵循五阶段控制模型:
塑化阶段:料筒四段温控(后段190℃/中段210℃/前段230℃/喷嘴220℃)
注射阶段:采用多级注射压力控制(一级120MPa充填90%型腔,二级80MPa补缩)
保压阶段:按PVT曲线实施梯度保压,补偿6-12%的体积收缩
冷却阶段:模温机控温±1℃,冷却时间=制品最厚壁厚²×1.5(单位:s/mm²)
顶出阶段:配置氮气弹簧辅助顶出系统,顶杆速度控制0.5-1.2m/s
通过闭环控制系统(CPK≥1.67),各阶段参数波动可控制在±1.5%以内。
注塑设备
塑料注射成型所使用的设备专为满足该工艺的高强度、高精度需求而设计,确保生产过程中的稳定性和一致性。
注塑机的主要组成部分
一台注塑机通常由三个主要部分组成:注射单元、锁模单元和液压系统。
注射单元:负责将塑料加热熔融,并以高压注入模具型腔。
锁模单元:用于固定模具,并在注射过程中施加足够的锁模力,确保模具严密闭合,防止材料外泄。
液压系统:为机器提供动力,控制注射单元和锁模单元的运动,实现各项操作的精确执行。
注塑机的类型
注塑机根据结构形式可分为卧式注塑机和立式注塑机两大类:
卧式注塑机是最常见的类型,适用于各种常规注塑加工,具有操作便捷、自动化程度高、应用范围广等优点。
立式注塑机则多用于嵌件注塑工艺,如将金属嵌件或其他零部件预先放入模具中,再进行注塑成型。该类型设备更适合需要人工或机械手配合的精密嵌件成型作业。
不同类型的注塑机各有优势,需根据产品结构、生产工艺及自动化需求等因素综合选择,以实现最佳的生产效率与成品质量。
注塑工艺参数控制
塑料注射成型的质量与生产效率在很大程度上取决于各项工艺参数的精确控制。合理设定和调节这些参数,是实现高质量注塑成品的关键。
温度控制
温度控制对于塑料的流动性和成型后的冷却固化至关重要。
料筒加热温度需要精确调节,以确保塑料熔融后具备合适的粘度,便于顺利注入模具型腔。
模具温度同样需保持稳定,以利于塑料材料的均匀冷却,减少翘曲、缩水等成型缺陷的发生。
科学的温度控制能够显著提升产品的一致性与外观质量。
注射压力与注射速度
注射压力和注射速度是决定型腔充填程度和成型质量的关键参数。
高注射压力可确保模具型腔被充分填满,避免出现短射或空洞现象。
注射速度则直接影响塑料的流动路径与冷却速度,速度过快易产生毛边(披锋),过慢则可能导致填充不足。
因此,需要在注射压力与速度之间取得合理平衡,以实现稳定的生产效果。
保压时间与冷却时间
保压时间与冷却时间对最终成品的尺寸精度与表面质量有显著影响。
保压时间是指在注射完成后,继续向模具内施加压力的时间,以补偿材料冷却时产生的体积收缩,确保型腔被充分充实。
冷却时间是熔融塑料在模具中冷却至足够强度、可顺利脱模的时间。
合理优化保压与冷却阶段,有助于缩短成型周期,提高生产效率,同时减少成品缺陷,提高产品合格率。
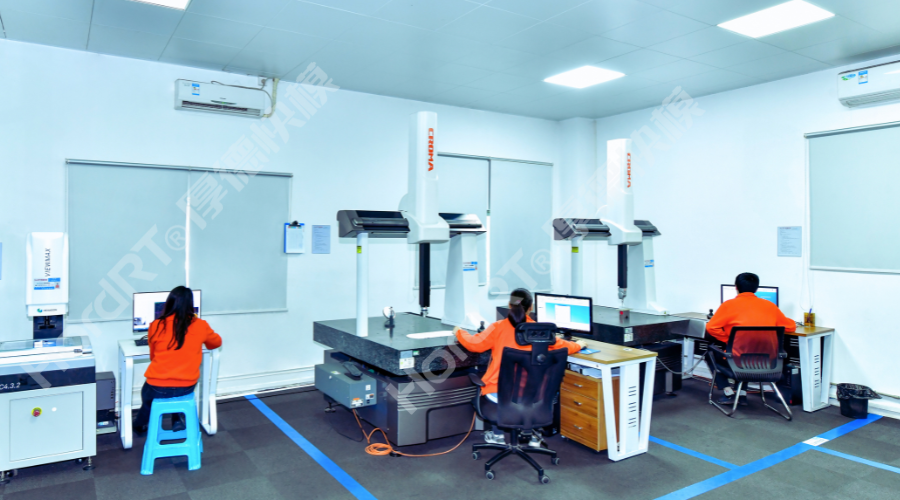
质量控制与缺陷分析
在注塑生产中,维持高质量标准需要完善的质量控制方法和对潜在缺陷的深入理解。
质量控制方法
注塑成型的质量控制主要包括统计过程控制(SPC)、目视检验以及尺寸分析等手段。
统计过程控制(SPC):通过分析生产过程中采集的数据,实时监控工艺状态,及时发现偏差,有效控制产品一致性。
目视检验:用于快速识别表面缺陷,如毛边、气泡、变形等。
尺寸分析:则借助测量工具和仪器,确保产品各项尺寸符合设计要求。
通过系统化的质量控制手段,可以在早期识别问题,避免大批量不良,提高整体生产效率与产品可靠性。
常见缺陷及解决方案
注塑成型过程中可能出现多种常见缺陷,如翘曲、缩水凹痕、气泡及短射等:
翘曲变形:多由冷却不均或收缩不均造成。
缩水凹痕:是由于材料在冷却过程中体积收缩,造成表面凹陷。
气泡:则是因气体未能完全排出,被困于产品内部所致。
短射则是因型腔未被完全填充,导致制品不完整。
解决这些问题通常可从以下几个方面入手:
优化工艺参数:如调整注射压力、速度、保压时间与冷却时间,有助于材料均匀填充与冷却。
改进模具设计:合理布局流道、排气口及冷却通道,有助于减少成型缺陷。
选用合适的材料:材料的流动性、收缩率等特性会直接影响成型效果。
例如,通过适当延长冷却时间和控制模温,可以显著降低翘曲与缩水凹痕的发生概率。
结论
塑料注射成型是一种工艺复杂但效率极高的制造方法,能够批量生产结构复杂、质量稳定的高精度零件。通过深入理解注塑成型的各个流程,并精准控制关键工艺参数,可以实现理想的成型效果,持续保持产品的一致性与优良品质。
中山厚德快速模具提供一站式塑料注射成型服务,依托先进的技术和丰富的行业经验,致力于为客户定制高质量、高精度的塑料制品。我们的现代化生产设施和严苛的质量管理体系,确保每一个项目都符合最高标准。无论是原型开发还是大批量生产,德快速模具都是您值得信赖的合作伙伴,助力实现高效、可靠的注塑解决方案。