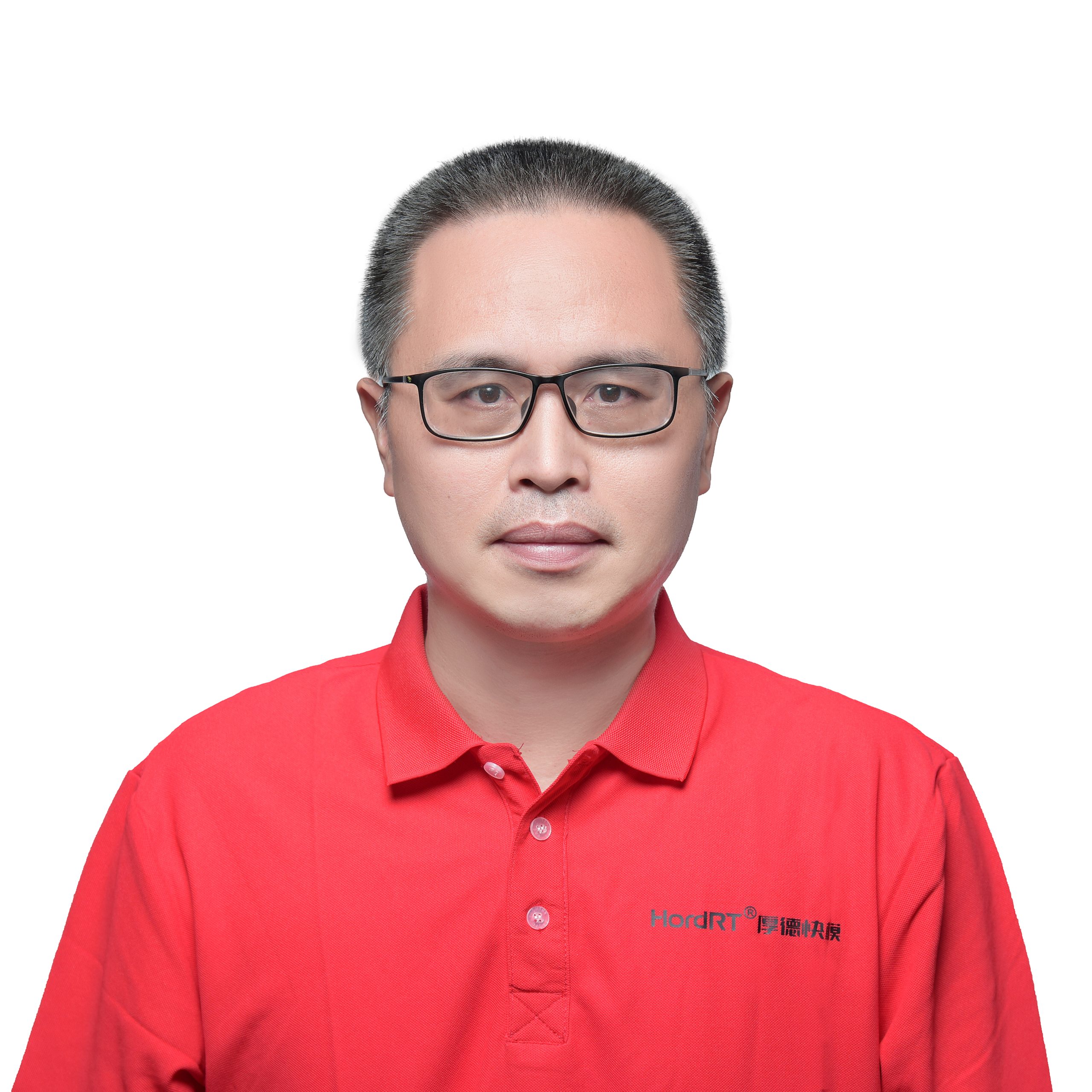
Johnny Xiong
Rapid Tooling Expert
Contents
在现代制造业中,注塑成型和挤出成型是两种最为常见且广泛应用的生产技术。它们各有特点,适用于不同的项目需求。本文将深入分析这两种工艺的区别、优缺点及其适用场景,帮助您做出明智的选择。
注塑成型与挤出成型的区别
注塑成型
注塑成型(Injection Molding)是一种常用的塑料加工方法,通过将塑料原料加热至熔融状态后,注入模具腔内,经过冷却固化后形成所需的塑料制品。这种工艺非常适合批量生产具有复杂形状的产品,广泛应用于汽车、电子、家电、医疗等行业。
注塑成型的优缺点
优点
- 复杂设计:注塑成型能够制造复杂的三维零件,适合具有复杂形状和精度要求的部件。
- 规模化生产优势:注塑成型在大规模生产时具有显著的成本效益,生产规模越大,单件成本越低。
- 材料选择广泛:该工艺可以使用多种塑料材料,满足不同的力学、热学和化学性能要求。
缺点
- 初期投资较高:注塑成型的模具和模具开发需要大量的前期投资。
- 产品尺寸的限制:注塑成型适用于小到中等尺寸的零件,对于大型复杂产品的生产,注塑可能无法满足要求,或者需要非常庞大的模具。
挤出成型
挤出成型则用于生产具有恒定截面的长型零件。通过将熔融材料强制挤出通过模具,形成如管材、型材或板材等产品。挤出成型的特点是高效、连续生产,且适用于批量生产简单的形状。
挤出成型的优缺点
优点
- 连续生产:挤出成型适合生产长型零件,如塑料管材和窗框,能够确保高效和稳定的生产。
- 低模具成本:与注塑成型相比,挤出成型的模具费用较低,非常适合生产简单型材。
- 材料效率:挤出成型可最大程度减少材料浪费,降低成本,并提升可持续性。
缺点
- 形状复杂度受限:挤出成型不适合制造复杂几何形状,精度要求较高的零件。
- 表面处理需求:挤出的零件表面可能需要额外的处理,以达到光滑效果。
- 强度不均匀:由于挤出过程的特性,材料的强度可能沿着挤出方向发生变化。
注塑成型与挤出成型的详细对比
零件复杂度
- 注塑成型:能够制造复杂的设计,包括带有倒角、孔洞和纹理的零件。
- 挤出成型:仅适用于简单且具有均匀截面的形状。
生产规模
- 注塑成型:适合批量生产,特别是大规模生产时,具有显著的成本优势。
- 挤出成型:适用于连续生产长型产品,如管道或型材。
模具成本
- 注塑成型:虽然初期模具成本较高,但对于大规模生产,长期来看是具有成本效益的。
- 挤出成型:模具成本较低,但在设计变更方面的灵活性较差。
应用领域
- 注塑成型:广泛应用于汽车、消费电子、医疗设备等需要高精度零件的行业。
- 挤出成型:适用于生产塑料管、窗框、型材等需要均匀截面的长型产品。
结论
注塑成型与挤出成型在制造业中各自占有重要地位,二者各有优势与局限。对于需要高精度和复杂三维设计的零部件,注塑成型无疑是更为合适的选择,尤其是在大规模生产时。而当需求集中在简单、长型零件时,挤出成型则显得更加高效且具成本优势。如果您的项目需要快速、高效的生产复杂零件,注塑成型将是最佳选择。然而,对于需要制造简单形状的长型产品,挤出成型则更具优势。
在厚德快模,我们专注于注塑成型,凭借多年的技术积累和高效的生产能力,我们为客户提供定制化、高质量的零件制造解决方案。如果您对制造工艺选择有任何疑问,我们的专业团队将为您提供最佳的建议与支持。