注塑成型是一种重要的制造工艺,广泛应用于多个行业。该工艺通过高压将熔融的材料(通常为树脂)注入金属模具的型腔中,待材料冷却后,顶针会将成品件从模具中顶出。
合理的可制造性设计可以加快生产周期,降低制造成本。基于我们在注塑成型方面的丰富经验,我们整理了一系列设计建议,旨在帮助您提升零件的可制造性。内容涵盖壁厚、脱模斜度、加强筋等关键设计因素,有助于提高零件的成型性,降低生产过程中的异常风险、美观缺陷以及其他潜在问题。
1. 壁厚设计
获得高质量注塑件最重要的设计原则之一,就是保持壁厚的一致性。过厚的部位容易导致缩水、变形,甚至使零件尺寸不准或无法正常使用。
设计壁厚一致性的优势:
材料流动更顺畅
冷却和收缩更加均匀
降低变形风险
减少模内应力
通过降低零件的最大壁厚,可以有效缩短成型周期(尤其是注射和冷却时间),同时减少材料用量,从而降低生产成本。
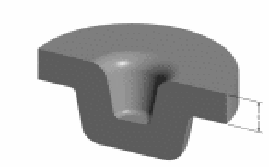
错误示范
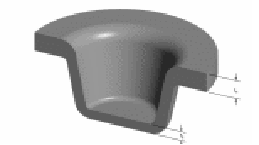
错误示范
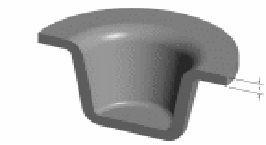
正确做法
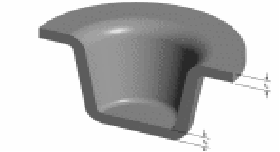
正确做法
2. 脱模斜度设计
在进行注塑件设计时,给零件的垂直面添加适当的脱模斜度至关重要。脱模斜度有助于零件在成型后顺利从模具中脱出,避免粘模现象。
如果没有设计足够的脱模斜度,零件不仅可能出现划痕、变形、甚至断裂,还可能影响外观质量,这些问题通常源于塑料冷却收缩时产生的模内应力。
需要注意的是,脱模斜度的大小应根据材料类型、壁厚、零件结构形状以及收缩率等因素综合确定。合理的斜度设计可提升产品品质,并延长模具寿命。
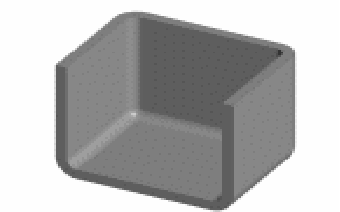
错误示范:未添加脱模斜度
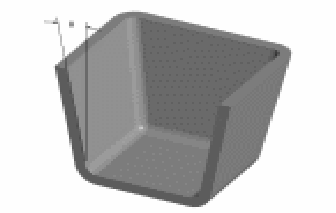
正确做法:添加脱模斜度
3. 加强筋设计
为了避免出现凹陷痕,增强筋的厚度应保持在名义壁厚的50%-60%之间。增强筋的高度应约为名义壁厚的2.5到3倍。
增强筋应用于提供结构支撑,而不是通过增加壁厚来增强强度。
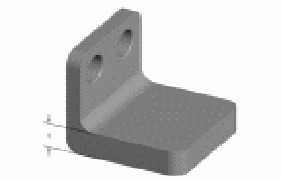
错误示范
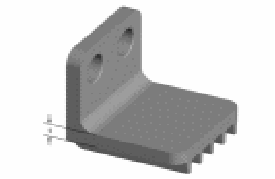
正确做法
如果增强筋与轴线垂直,可能会导致弯曲变形。
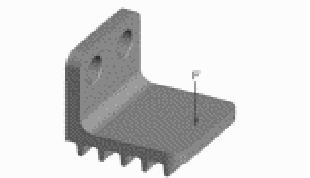
错误示范
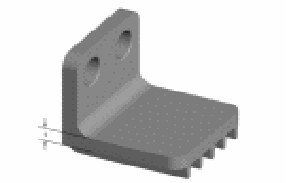
正确做法
4. 加强柱设计
加强柱是指零件上突出的支柱,用于帮助塑料零件与其他部件的组装。它们可用于压入式组装、自攻螺钉组装、或标准机械螺钉的螺纹连接。
加强柱的壁厚应不超过主壁厚的60%。
加强柱底部的半径应至少为主壁厚的25%。
应通过与相邻壁连接的加强筋或基部的肋板来支撑。
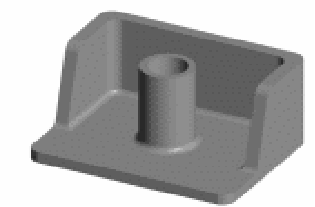
错误示范——孤立的加强柱
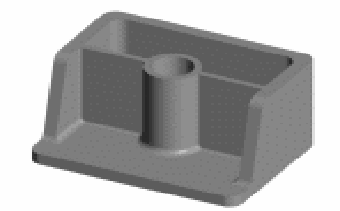
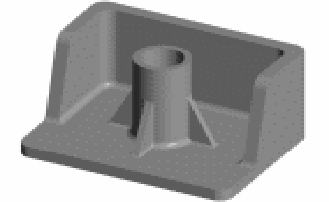
正确做法——带有加强筋(左)或肋板(右)的孤立加强柱
如果必须将加强柱放置在角落附近,应该使用加强筋将其与其他部件隔离。
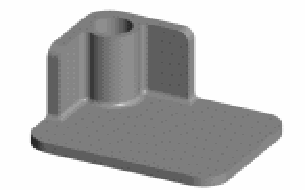
错误示范——角落中的加强柱
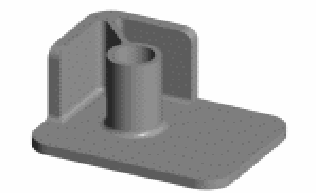
正确做法——角落中的带肋加强柱
5. 圆角设计
尖锐的角落会导致高应力集中,同时阻碍塑料的流动。通过设计圆角,可以减少模具部件的应力集中,并为熔融塑料提供更加流畅的流动路径,从而更容易填充模具。
圆角设计应始终考虑零件的壁厚,以避免出现高应力区域并减少零件破裂的风险。
一般的经验法则是,角落处的厚度应保持在名义壁厚的0.9倍到1.2倍之间。
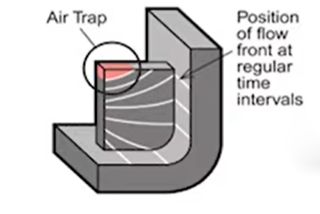
错误示范
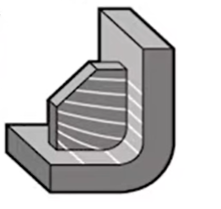
正确做法
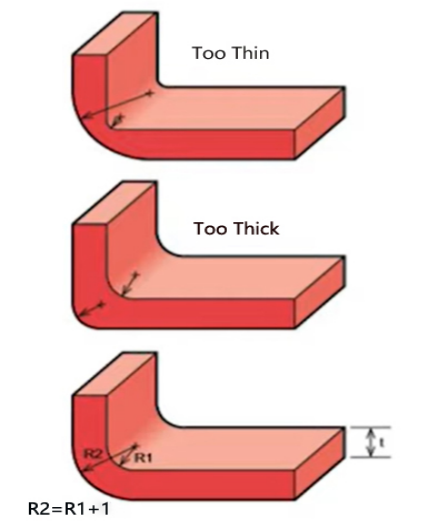
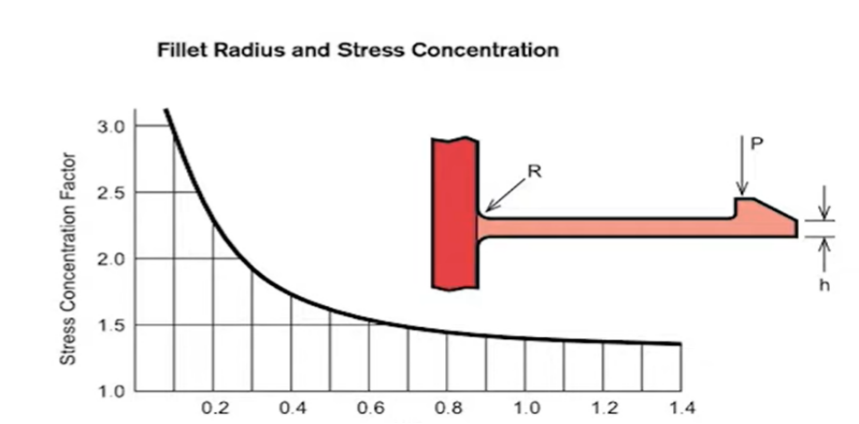
6.凹陷设计
凹陷是指那些在没有结构损伤的情况下,阻止注塑件从模具中顺利脱模的特征。在设计零件时,应该注意以下几点:
尽量减少外部凹陷的数量
外部凹陷需要侧模芯,这会增加模具成本
一些简单的外部凹陷可以通过调整分模线来实现成型

简单外部凹陷
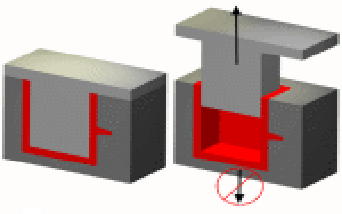
模具无法分离
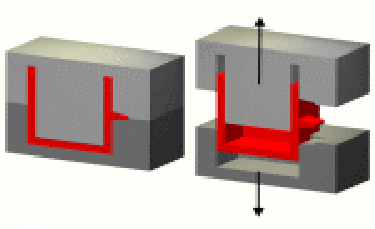
新的分模线允许凹陷成型
重新设计一个特征可以去除外部凹陷。
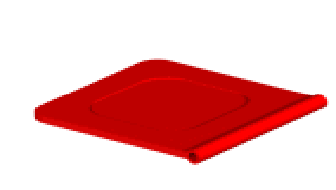
带有铰链的零件
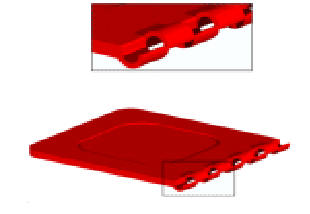
带有铰链的零件
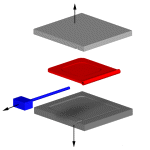
铰链需要侧模芯
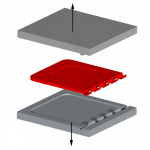
新的铰链设计可以成型
尽量减少内部凹陷的数量
内部凹陷通常需要内部模芯提升器,这会增加模具成本
在零件侧面设计开口可以使侧模芯形成内部凹陷
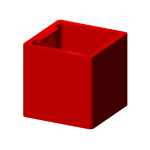
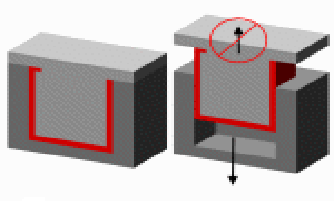
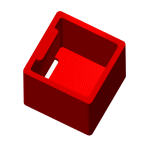
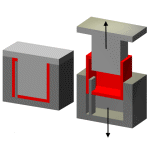
如果您有任何新项目,请随时通过 rfq@hordrt.com 与我们联系。